Figure 1 From Anomalous Deformation Twinning In Fcc Metals At High
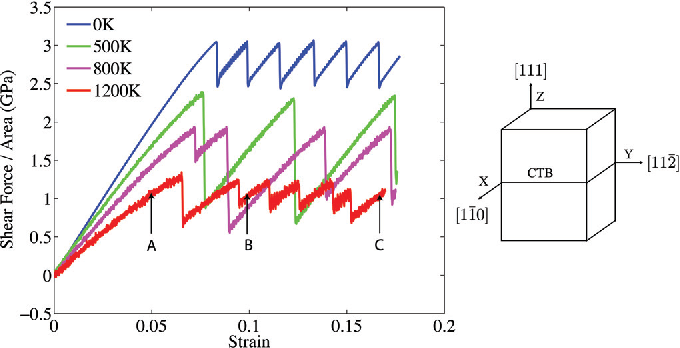
Figure 1 From Anomalous Deformation Twinning In Fcc Metals At High At low and intermediate temperatures, the twin boundaries exhibit normal motion coupled to shear deformation as expected. however, our simulations at higher temperatures (above 0.5–0.7 t m), reveal considerable deformation twinning, an occurrence that has not been observed before in fcc metals. although the origins of this intriguing behavior. Defor mation twinning refers to the formation of a pair of ctbs under deformation. this is a two step process, as illustrated in fig. 5(b). section ii presents the details of our simulations and results. in sec. iii, we analyze our results based on the ener getics of these competing mechanisms and discuss a possible.

Schematic Illustration For Slipping And Twinning Modes Of Fcc Metals Deformation as expected. however, our simulations at higher temperatures (above 0.5–0.7 t. m. ), reveal considerable deformation twinning, an occurrence that has not been observed before in fcc. Fig. 1. (color) shear stress vs strain plots for cu bicrystals at various temperatures, and the crystallographic orientation of the bicrystals. the atomic structures at a, b, and c are shown in fig. 4. "anomalous deformation twinning in fcc metals at high temperatures". Anomalous deformation twinning in fcc metals at high temperatures. nanotwinned structures have shown strong promise as optimal motifs for strength, ductility, and grain stability in fcc metals—in sharp contrast to their nano grained counterparts where gains in strength are disappointingly offset by loss of ductility. Other factors on deformation twins. beside above discussed factors, thermal treatment, texture and second phase particles can also influence the deformation twinning in bcc metals and alloys [198], [250], [255], [259]. these factors, to some extent, are closely related to the factors we discussed above.

Schematic Illustration For Slipping And Twinning Modes Of Fcc Metals Anomalous deformation twinning in fcc metals at high temperatures. nanotwinned structures have shown strong promise as optimal motifs for strength, ductility, and grain stability in fcc metals—in sharp contrast to their nano grained counterparts where gains in strength are disappointingly offset by loss of ductility. Other factors on deformation twins. beside above discussed factors, thermal treatment, texture and second phase particles can also influence the deformation twinning in bcc metals and alloys [198], [250], [255], [259]. these factors, to some extent, are closely related to the factors we discussed above. Deformation modes in metals and alloys ! twinning in fcc metals (part 1) ! twinning in bcc metals (part 2) twinning stress in smas twin nucleation model ! peierls nabarro (p n) formulation ! energy landscape (gpfe) in ni 2fega ! twin nucleation model based on p n formulation 22 outline!. The plastic deformation mechanisms that govern the mechanical performance of crystalline metallic materials include dislocations, twinning, stacking faults, and displacive phase transformations 1.

Twinning In Fcc Metals High Temperature Materials Laboratory Illinois Deformation modes in metals and alloys ! twinning in fcc metals (part 1) ! twinning in bcc metals (part 2) twinning stress in smas twin nucleation model ! peierls nabarro (p n) formulation ! energy landscape (gpfe) in ni 2fega ! twin nucleation model based on p n formulation 22 outline!. The plastic deformation mechanisms that govern the mechanical performance of crystalline metallic materials include dislocations, twinning, stacking faults, and displacive phase transformations 1.
Comments are closed.