Chiller Energy Savings Based On Historic Load The Engineering Mindset
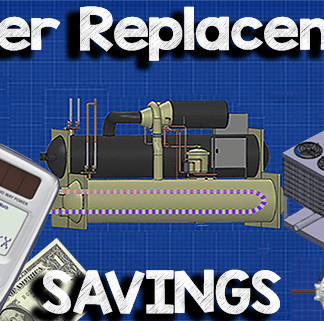
Chiller Energy Savings Based On Historic Load The Engineering Mindset By multiplying the efficiency by the cooling load, we get the hourly kwh consumption. chiller replacement, based on historic load kw ton. then we can see that the existing chiller would consume 1,378 kwh a day whereas the new potential chiller would consume 980 kwh a day resulting in a saving of 398 kwh. The amount you can save really depends on how much fouling has built up on the surfaces. cleaning heavily fouled chiller could lead to an energy saving of up to 10% where as a lightly fouled chiller would see 1 3% improvement. this is going to depend on how much fouling builds up as well as how long the chillers run.
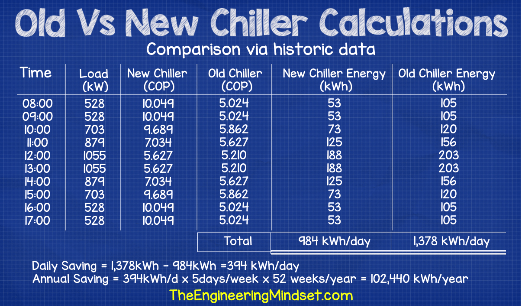
Energy Savings From Replacing A Chiller The Engineering Mindset Base model values represent a 100 ton air cooled electric chiller operated for 2,000 full load hours per year with an eer of 9. the performance of this standard unit is based on ashrae standard 90.1. How to calculate energy savings from replacing a chillerchiller iplv is the rating based on a loop temperature of 44f. many chiller manufacturers such as chiltrix also offer an nplv rating. nplv stands for non standard part load value. in addition to iplv, chiltrix uses an nplv rating for loop water temperature of 55f. By analyzing operating data, the chiller with higher cop was selected and given the priority to be turned on for cooling supply. the cop of the 2# chiller was about 0.3 higher than that of the 1# chiller on average. this also proves that the main source of energy saving for chillers came from changing the loading sequence. 4.2.2. The slightest decrease in chiller performance can have a major impact on efficiency. for instance, every 1°f increase in condenser water temperature above full load design can decrease chiller efficiency by 1% to 2%. a failing or neglected water treatment program can reduce efficiency 10% to 35% or more in extreme cases.
Comments are closed.